Gas chromatography doesn’t just live in pristine labs—it also operates in gritty industrial plants. While both online (process) and laboratory gas chromatography (GC) systems separate chemical mixtures, their daily routines couldn’t be more different. Let’s explore how “process gas chromatographs” like the “HPGC-1000 Process Gas Chromatograph” tackle challenges lab instruments can’t handle.
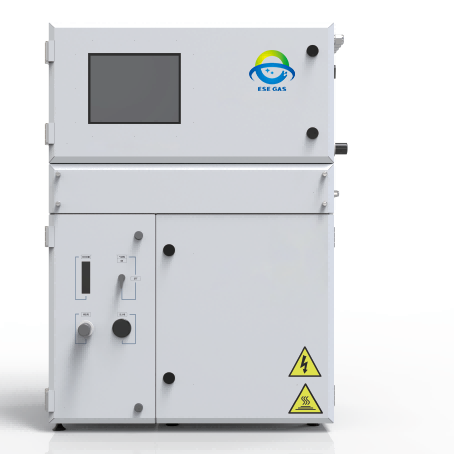
Comparison Between Online Chromatography and Laboratory Chromatography
Comparison Criteria | Online Chromatography | Laboratory Chromatography |
Purpose | Process monitoring/control; multi-purpose applications. | Batch analysis; offline measurements. |
Measurement Type | Continuous, in-line monitoring. | Discrete batches; offline analysis. |
Injection Method | Primarily valve injection with a quantitative loop for sample volume control. | Valve injection, autosampler trays, headspace, direct syringe injection, etc. |
Analytes | Targeted components (specific compounds or groups). | Broad range of components (non-specific or multi-component analysis). |
Automation & Monitoring | Fully automated operation from injection to data recording; trend tracking without manual intervention. | Requires operator intervention for setup, analysis, and data handling; higher labor costs. |
Sampling | Automated sampling systems integrated with processes. | Manual or semi-automated sampling. |
Analysis Cycle | Fast (optimized for real-time process feedback). | Slower to moderate (dependent on manual steps and method complexity). |
Design | Explosion-proof construction for hazardous industrial environments. | Non-explosion-proof, suited for controlled laboratory settings. |
Data Transmission | Direct integration with Distributed Control Systems (DCS); continuous, stable data output with trend tracking capabilities. | Manual data collection, processing, and reporting; requires post-analysis data handling. |
Operator Expertise | Operated by automation/control engineers with limited chemistry knowledge; emphasis on system integration and reliability. | Operated by analytical chemists with strong technical expertise; minimal automation requirements. |
Sample Handling & Representativeness | Advanced sample pretreatment systems ensure representative sampling and minimal contamination (e.g., for reactive or trace analytes). | Limited sample pretreatment; risk of adsorption, contamination, or non-representative results (e.g., sulfur compounds, liquid-carrying gas samples). |
Instrument Flexibility | Customizable configurations (multi-stream, multi-channel) for diverse sample types; fixed functionality during operation. | High flexibility post-configuration; advanced data processing via chromatography workstations. |
How Do Process Gas Chromatographs Handle Continuous Monitoring While Lab Systems Focus on Precision?
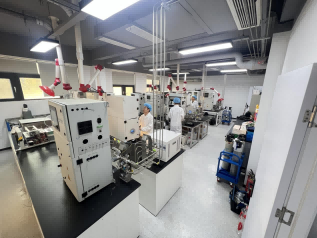
In industrial settings, online gas chromatography (GC) operates as a 24/7 watchdog. Unlike lab instruments, process gas chromatographs automatically sample gas streams every 15-30 minutes. No human hits the “start” button—these systems crank out real-time data to control panels, helping operators tweak valves before product quality drifts. Missing single peak detection could risk flammable vapor buildup overnight. In contrast, lab gas chromatography GCs rely on scientists to manually prepare samples for detailed analysis, often requiring hours to identify contaminants in pharmaceuticals or drinking water.
Imagine a natural gas processing plant operating at -10°C. The HPGC-1000 Process Gas Chromatograph thrives here with its explosion-proof rating (Ex db eb mb pxb II C T4 Gb) and vibration-resistant design. Unlike lab GCs requiring stable environments, this workhorse handles ambient temperatures from -10°C to 40°C while maintaining ±0.05°C oven control. Its gas-bath heating technology ensures stable separations even during pipeline pressure fluctuations.
Why Do Industrial Environments Demand Ruggedized gas chromatography Solutions?
Imagine a natural gas processing plant operating at -10°C. Process gas chromatographs wear armored suits—explosion-proof housings that let them breathe toxic atmospheres without sparking disasters. The HPGC-1000 thrives here with its explosion-proof rating (Ex db eb mb pxb II C T4 Gb) and vibration-resistant design.
Lab systems prioritize ultra-fine capillary columns for trace pesticide detection.Their delicate capillary columns can detect parts-per-billion traces of pesticides in food, but ask them to analyze a sulfur-laden natural gas stream? However, the HPGC-1000 combines packed, micro-packed, and capillary columns to analyze complex streams containing H₂S, methane, or heavy hydrocarbons. With 40L thermostatic chambers and capacity for 10 sampling valves, it performs continuous multi-stream monitoring—a task that would overwhelm most laboratory GCs.
Can Process Gas Chromatographs (GCs) Deliver Both Speed and Precision?
Online systems play beat-the-clock. A petrochemical plant’s GC might complete 30 analyses an hour, its data feeding directly into control loops. Slow down? That delayed feedback could cost thousands in off-spec product. Lab systems may spend hours separating 50+ components in pharmaceutical impurities.A forensic toxicologist might run a 90-minute gradient to separate 25 drug metabolites from blood. For these detectives, thoroughness trumps speed—every peak tells a story.
How Often Should Process Chromatographs Be Calibrated?
Field units like the HPGC-1000 require frequent validation due to harsh conditions. However, its integrated hydrocarbon remover and methane converter extend calibration intervals by 40% compared to standard models. The system’s ≤1% hourly drift (across all detectors) ensures reliable data between validations—critical for continuous emissions monitoring systems (CEMS).
Lab instruments stay validation-ready for weeks. Their secret? Controlled environments. No wild temperature swings, no particulate-clogged lines—just steady work analyzing everything from whiskey aromas to microplastic pyrolysis products.