You’d be surprised how often that plastic water bottle or vinyl siding owes its quality to an unsung hero in the lab. Process gas chromatographs (PGCs) don’t just analyze chemicals—they’re the ultimate quality guardians in manufacturing. Walk through any modern chemical plant, and you’ll find chromatographs working overtime. These aren’t your grandpa’s lab tools—they’re sophisticated systems separating chemical cocktails with surgical precision. Imagine trying to spot a single wrong note in a symphony; that’s what PGCs do daily for product batches.
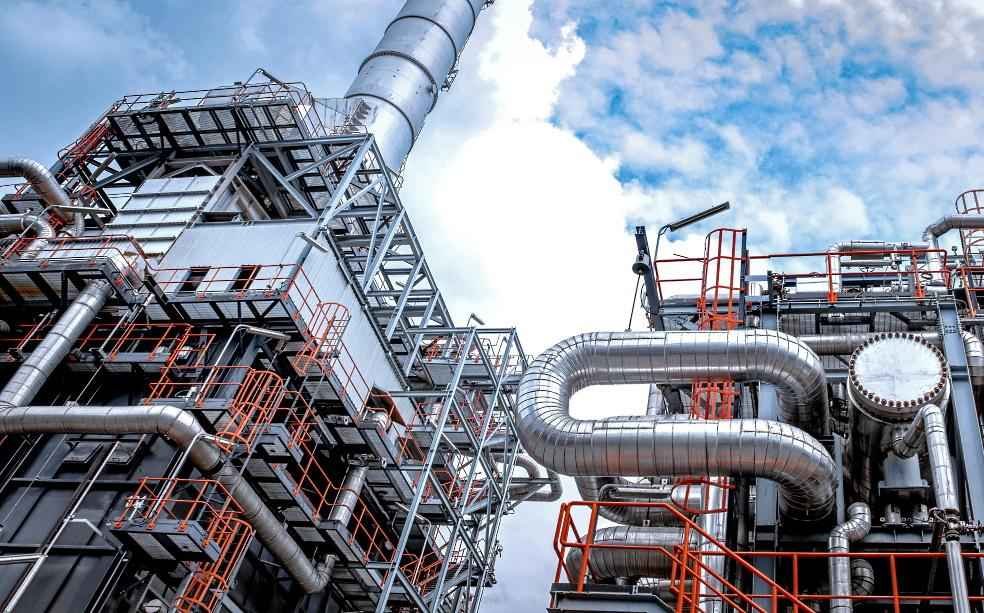
Modern industrial operations demand real-time monitoring solutions like the HPGC-1000 Process Gas Chromatograph from ESEGAS. This analytical powerhouse handles gases and vaporizable liquids across industries—from natural gas processing to pharmaceutical production. Unlike traditional lab instruments, its PID-controlled air bath heating maintains ±0.05°C accuracy in a 40L thermostatic chamber, ensuring stable separation even in harsh environments (-10°C to 40°C).
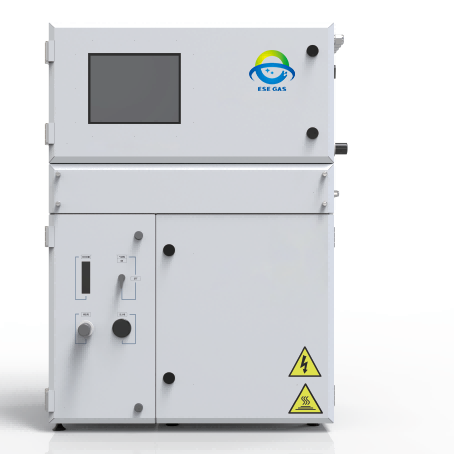
(HPGC-1000 Process Gas Chromatograph)
What Makes the HPGC-1000 a Versatile Process Gas Chromatographs?
Process Gas Chromatographs (PGCs) shine through sniffing out rogue molecules at parts-per-billion levels. Petrochemical plants live by this tech too—analyzing 40+ component gasoline blends demands separation superpowers only chromatography delivers. With configurable detectors (TCD, FID, FPD, PDHID) and multi-detector setups, this system achieves remarkable sensitivity. For instance, its FID detects methane down to 15 ppb, while the PDHID reaches 10 ppb—critical for tracking trace impurities in specialty gases.
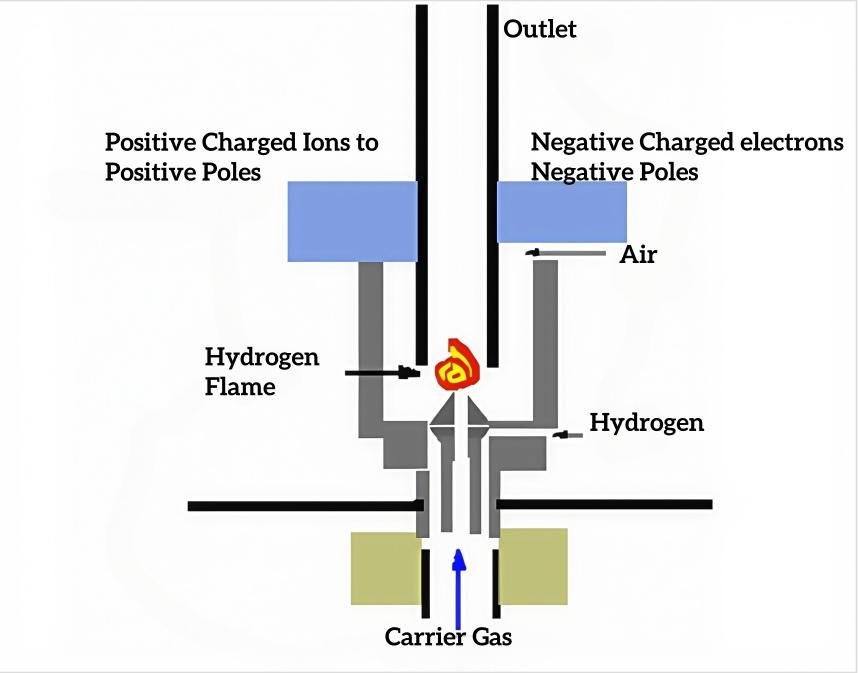
(HPGC-1000 Process Gas Chromatograph’s FID working principle)
But it’s not just about catching errors. During solvent production, real-time PGC data guides adjustments like a master brewer tweaking fermentation. Operators can install up to 10 sampling valves and choose packed, micro-packed, or capillary columns, enabling tailored configurations for complex streams like refinery gas or ethylene cracker effluents.
Why Do Process Industries Prioritize Stability in Gas Analysis?
Those “new car smell” chemicals? Gas chromatographs ensure they won’t gas you with VOCs. When a Midwestern plant recently traced mysterious odors to contaminated plasticizers, their GC-MS combo identified the culprit—a degraded stabilizer—in under an hour.
Consistency separates adequate instruments from exceptional ones. The HPGC-1000 Process Gas Chromatograph delivers ≤±1% F.S. repeatability error and ≤1% hourly zero drift across all detectors—vital for maintaining ISO-compliant quality control. During catalyst regeneration cycles or methanol synthesis, such precision prevents costly deviations. Moreover, its explosion-proof design (Ex db eb mb pxb II C T4 Gb) ensures safe operation in hazardous zones common to petrochemical plants.
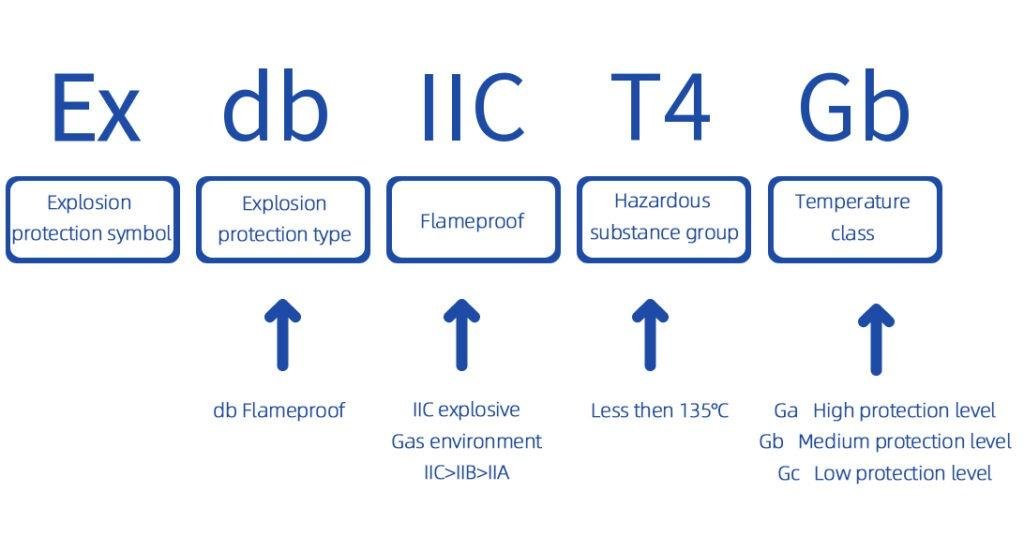
How Do Modern Process Gas Chromatographs Enhance Operational Efficiency?
Food manufacturers play this game too. That vanilla extract in your cookies? GC analysis verifies authenticity, distinguishing natural vanillin from cheaper lignin-derived versions. It’s flavor forensics, ensuring your $8 ice cream stays premium.
Beyond analysis, the HPGC-1000 integrates seamlessly with plant systems. Its Modbus-enabled I/O (8 AI, 12 AO, 8 DI/DO) and 10.4-inch HMI allow real-time data sharing with distributed control systems. When analyzing multi-component streams like LNG or syngas, the optional methane converter extends measurement ranges while hydrocarbon removers reduce interference. With N₂/He carrier gas consumption optimized at 30-300 ml/min (99.999% purity), labs cut operational costs without sacrificing accuracy.
Can Process Gas Chromatograph Systems Future-Proof Industrial Operations?
Newer PGCs (Process Gas Chromatograph) are getting smarter—imagine instruments that self-calibrate using AI-driven pattern recognition.
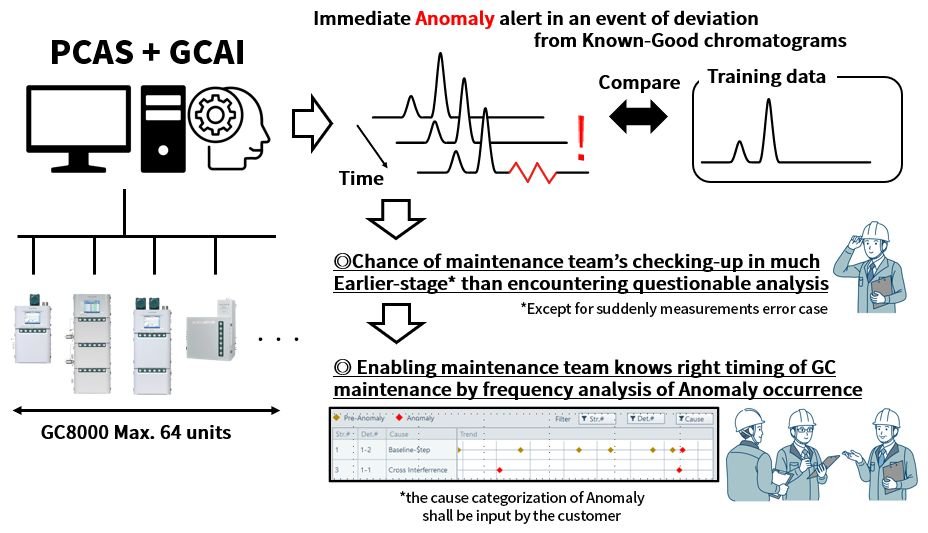
(GCAI)
Forward-thinking plants use GC (Gas Chromatography) data to predict catalyst lifetimes, turning analytical tools into profit engines. As one tech puts it: “We’re not just testing products anymore—we’re crystal-balling the whole process.”
As industries adopt Industry 4.0, the HPGC-1000 Process Gas Chromatograph’s Ethernet connectivity supports predictive maintenance strategies. Its ability to monitor 100% concentration ranges (from ppb levels) helps plants transition to hydrogen economy applications. For example, detecting 100 ppm CH₄ in H₂ via TCD ensures fuel cell-grade purity. With dual FID or quad TCD configurations, operators gain redundancy for mission-critical processes—a key advantage over single-detector systems.
Conclusion
Next time you see a chemical tanker, remember—inside those pipes flows liquid gold vetted by chromatographs. They might not get headlines, but in the chemical world, GC isn’t just equipment—it’s insurance against catastrophe.
The HPGC-1000 exemplifies why process gas chromatographs remain indispensable in industrial analytics. By combining rugged construction (-10°C to 180°C operability) with cutting-edge detection limits, ESEGAS’ solution doesn’t just measure compounds—it safeguards profitability and compliance in an era of tightening emission regulations. For plants aiming to optimize hydrocarbon processing or specialty gas production, this instrument delivers the analytical confidence needed to stay competitive.